The benefits of process optimization are not exclusive to large businesses alone since any business can actually benefit from the process of optimization.
Many businesses want to increase their operational efficiency and improve how they execute their critical processes to gain a competitive advantage. To be successful, they must focus on first-to-market, cost-competitiveness, quality and customer service strategies.
Business process optimization allows a business to scale in all areas, address continuous improvements, and increase performance quality. It may also involve the introduction of enhancements such as automation to improve efficiency.
“When patterns are broken, new worlds emerge” – Tuli Kupferberg
What is the Process of Optimization?
The word “optimize” means to make something as good, as efficient, as useful, or as functional as possible. It helps businesses reach their full potential and is just like getting a “tune up for the car” to increase and maximize its performance. Sometimes this may involve automation.
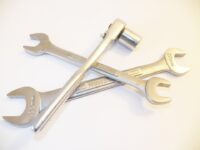
Process optimization helps your business to maximize efficiency, reduce costs, time and resources invested in addressing bottlenecks and mistakes, so the business can meet its strategic goals and expand market reach.
Focus Areas For Process Optimization
Business process optimization initiatives will differ between businesses and largely depends on the competitive environment of the industry in which they operate.
For example, focus areas are seen to differ in the following industries:
- Manufacturing companies: Customer service, access to information and supply chain management
- Service industries (engineering, geomatics, administrative): Customer service and quality processes are important
- Financial services (banks, insurance, brokerages) and government sectors: Customer service is the top priority to provide customer friendly portals for access to information, personal financial management and purchase of financial products.
- Educational bodies (schools): Access to data, and document and data management are key focus areas, as everything centers around data
The Problem
Your business consistently spends time fixing operational bottlenecks and correcting errors. This may happen in-house during production OR, worse still, faulty products manage to get through to the customer resulting in a lot of back-and-forth.
As a result, this negatively affects your profit margin, destroys competitive edge and creates employee frustration. Obviously, the customer experience from this kind of scenario could potentially result in loss of that customer.
This means a NON-RETURNING CUSTOMER, NO REFERRAL or TESTIMONIAL. What is the cost of the loss of that single customer to your business?
The Solution
There are standard Business Process Management steps for conducting process optimization. Quite honestly, you do not need to totally understand them. A summary is provided here solely for business owners who desire to know more about the work to be done.
To ensure overall company alignment a Six Sigma methodology integrated with the company goals is required to eliminate defects, correct errors and mistakes.
BENEFITS OF PROCESS OPTIMIZATION – DMAIC
It is generally recommended that the process optimization is initially implemented on a small scale. Once it is successful, it can be rolled out across other departments. Six Sigma employs DMAIC for these activities as summarized below:
- D = Define the Process Optimization Need that exists and create “current state” through process mapping because can only improve what you fully understand.
- M = Measure – Measure performance metrics for both the “current” and “future (proposed)” state processes.
- A = Analyze – Analyze the data to identify areas to make changes.
- I = Improve – Improve the process by re-design to the “proposed future state” so it is more efficient and use this to develop a process map. Identify the opportunities and improvements to optimize. A proposed solution may be automation.
- Implement the Optimized process – Launch the new process in the business. It is important that data is collected to analyze for the “future state”. This can only be successfully done by engaging the employees who use the process.
- C = Control – Establish control documents Assign process ownership for the process and establish controls. Monitor on a regular basis and apply continuous improvement principles.
This looks pretty straightforward, but it actually requires project management skills to ensure that each of the DMAIC phases are properly aligned. BCINC will provide the expertise to project manage your business process optimization process.
Eliminate Inefficient Processes And Automate
A key piece of Process Optimization is the elimination of inefficient processes and, automating as many tasks as are required. The key word is “required”, because not all businesses will require or desire process automation.
Automation is an area where a business must weigh the benefits to its organizational structure prior to taking a decision.
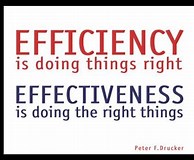
BENEFITS OF PROCESS OPTIMIZATION
Several benefits may be derived from optimizations and they include the following :
- Process mapping provides an easy visual overview to accurately understand the steps taken from input to output.
- Improved efficiency is the most obvious benefit of process optimization and this results in satisfied customers, lowered costs, higher revenue, and higher profit margins.
- Improved quality of all business processes ensures that there is consistency in product or service delivery.
- Waste reduction arises because redundancies and re-work are eliminated, while errors are reduced. This is a major benefit of Six Sigma. Waste reduction may require automation, but, this is not the only available tool.
- Easy access to accurate information because of improved data and document management
- Accountability because process owners and departmental accountabilities are defined
- Increased employee satisfaction and reduced turnover because of diminished frustration from inefficient processes
- Competitive advantage results in growth and increased market share.
- Identifies internal areas for improvement and investment – Continuous improvement and automation of certain repetitive tasks will make employees more productive since they will focus on those business tasks which enhance growth and additional areas for improvement are easily identified.
- Monitored performance is derived from the use of automated systems which promote proper reporting tools to reduce risks from human error.
- Communication between departments and functional units improve.
Final Words – Benefits of Process Optimization
The process of optimization creates valuable benefits in a business which include increased efficiency, profit margins and potential expansion of business market reach.
Contact us to schedule a No Obligation 30-minute Strategy Call about Business Process Optimization or other process challenges you may have
CLICK below