Despite the key role it plays, learning how to create an SOP document can be like navigating a minefield, with potential pitfalls lurking at every turn.
From unclear instructions to outdated procedures, the journey to SOP excellence is laden with challenges. However, with careful navigation and foresight, you can steer clear of these hazards and create SOP documents that are fit for purpose.
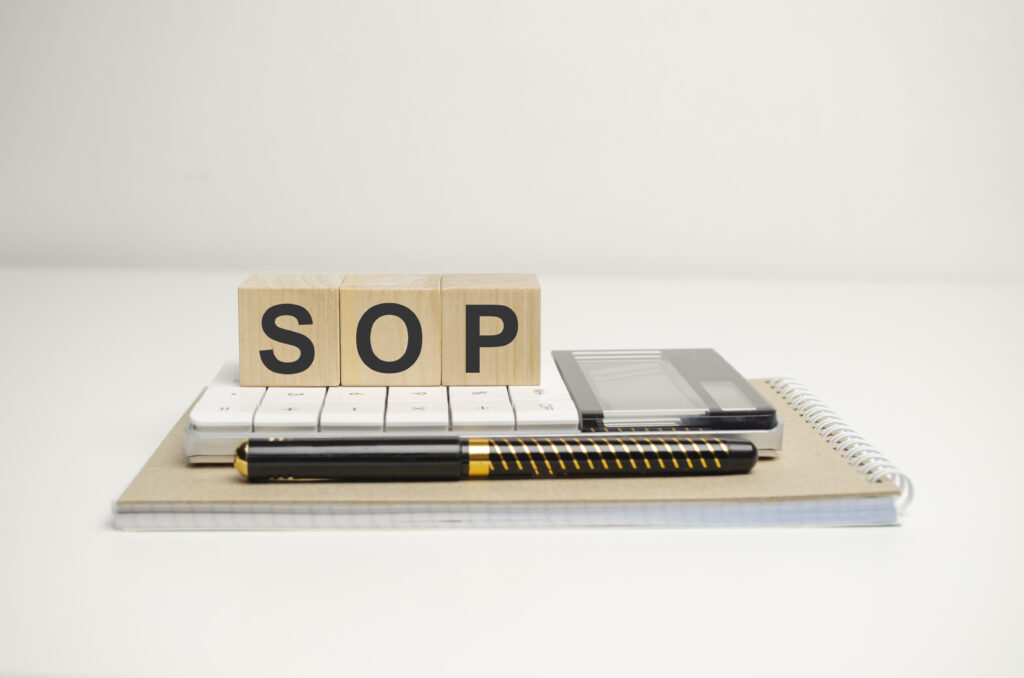
Understand the Purpose of SOP Documents
Before creating SOP documents, there is a need to fully understand the fundamental purpose of these documents. They serve as the blueprint for routine operations within any business, providing step-by-step instructions to ensure tasks are performed consistently and accurately.
Whether it is onboarding new employees, executing manufacturing processes, or handling customer inquiries, SOPs lay down the groundwork for operational success.
To avoid stumbling into the traps that often plague the creation of SOP documents, you must first recognize the advantages of standard operating procedures, and then their pitfalls.
Advantages of Standard Operating Procedures
Consistency and Quality Control: SOPs establish standardized processes for performing tasks or operations, ensuring consistency in output quality.
Efficiency and Productivity: SOPs streamline workflows by providing clear guidelines and step-by-step instructions for completing tasks to save time and resources.
Training and Onboarding: SOPs serve as valuable training tools for new employees, help accelerate the onboarding process providing them with structured guidance on how to perform their roles effectively. They offer a reference point for learning tasks and procedures.
Risk Management and Compliance: SOPs help mitigate risks associated with operational errors, safety hazards, and regulatory non-compliance. By outlining best practices and safety protocols, SOPs ensure that operations adhere to industry standards and legal requirements.
Decision Making and Problem Solving: SOPs provide a framework for decision making and problem solving by offering predefined solutions to common issues or challenges. Employees can refer to SOPs to troubleshoot problems and make informed decisions in their day-to-day work.
Improved Communication: SOPs facilitate communication and collaboration among team members by establishing a common understanding of processes and expectations. Clear documentation of procedures enhances communication channels within the organization.
Continuous Improvement: SOPs serve as a foundation for process improvement initiatives. By regularly reviewing and updating procedures, organizations can identify areas for optimization and implement changes to enhance efficiency and effectiveness.
Customer Satisfaction: Consistent adherence to SOPs leads to reliable product or service delivery, which ultimately enhances customer satisfaction. Customers can trust in the quality and reliability of the products or services they receive from the organization.
Resource Allocation: SOPs help optimize resource allocation by identifying the most efficient methods for completing tasks and allocating resources accordingly. This leads to better resource utilization and cost savings for the organization.
Business Stability and Scalability: SOPs contribute to business stability by providing a structured framework for operations. As businesses grow, SOPs support scalability by ensuring that processes remain standardized and manageable, even as the organization expands.
In summary, SOPs offer a wide range of advantages, including consistency, efficiency, risk management, and continuous improvement, making them indispensable tools for businesses striving for operational excellence.
Identify Common Pitfalls
Some common pitfalls include:
Overcomplication
SOPs should be clear and concise, avoiding unnecessary jargon or complexity that could confuse readers.
Lack of Clarity
Ambiguity in instructions can lead to misunderstandings and errors. You must be precise and unambiguous in detailing each step.
Neglecting Updates
As processes evolve, SOPs must evolve with them. Failure to update documents regularly can render them obsolete and ineffective. This is a major and very common pitfall.
Many think that all that is required is to create standard operating procedures once and then promptly forget all about them. Sadly, this sets the foundation for chaotic operations later in the business because of confusing implementation.
Create Standard Operating Procedure Without Ignoring Stakeholder Input
SOPs are most effective when they reflect the insights and experiences of those who actually execute the tasks. Failing to involve relevant stakeholders in the creation process can result in overlooked details or impractical procedures.
Even in a very small business, it is not advisable that a business owner single-handedly create SOPs without input from other employees that will use them.
Poor Formatting
A cluttered or disorganized layout can make SOPs difficult to follow. Consistent formatting, with clear headings and bullet points, enhances readability and comprehension.
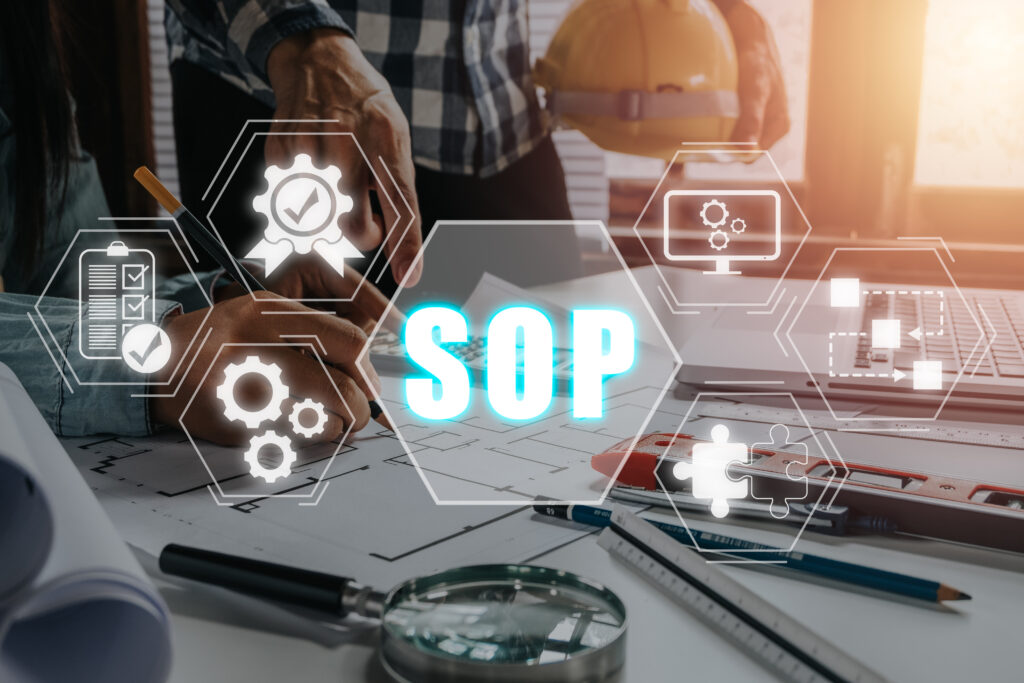
How to Create Standard Operating Procedures – Strategies for Success
Armed with an awareness of potential pitfalls, let’s explore strategies to navigate the SOP creation process smoothly:
Begin with a Clear Objective: Define the purpose and scope of the SOP document upfront. What specific process or task will it cover? What are the desired outcomes?
Gather Input from Stakeholders: Involve individuals directly involved in the process to provide insights and identify critical steps or nuances that should be included.
Keep It Simple: Strive for clarity and simplicity in language and structure. Use straightforward, action-oriented language and break down complex tasks into manageable steps.
Document Processes Accurately: Take the time to observe and document processes accurately, capturing every essential step and any potential variations or contingencies.
Regularly Review and Update: Set a schedule for reviewing and updating SOPs to ensure they remain current and reflective of evolving practices.
Seek Feedback: After drafting the SOP document, solicit feedback from stakeholders to identify any areas of confusion or improvement. Continuous refinement is key to optimizing effectiveness.
Provide Training: Once finalized, ensure all relevant personnel are trained on the SOPs to guarantee understanding and adherence.
Simple Standard Operating Procedure for Handling Rejects and Rework in a Small Manufacturing Business – Template Example
Rejects and Rework Standard Operating Procedure (SOP)
Objective:
The purpose of this SOP is to establish a clear process for handling rejects and rework in our small manufacturing company to maintain product quality and customer satisfaction.
Procedure:
1. Identification of Rejects:
- Inspect products during and after production for defects or deviations from quality standards.
- Label any defective or non-conforming products as rejects and document the reason for rejection.
2. Segregation and Documentation:
- Segregate rejected products from conforming products to prevent accidental shipment or use.
- Document details of the rejected products, including batch number, reason for rejection, and any relevant observations.
3. Evaluation for Rework:
- Assess whether rejected products can be reworked to meet quality standards.
- If rework is feasible and cost-effective, assign the task to qualified personnel.
4. Rework Process:
- Follow specific rework instructions provided for each type of defect or deviation.
- Ensure proper tools, materials, and equipment are available for the rework process.
- Monitor the progress of rework to ensure quality standards are met.
5. Re-inspection:
- After rework is completed, conduct a thorough inspection of the products to verify conformity to quality standards.
- If the products meet requirements, re-label them as conforming and update documentation accordingly.
6. Disposition of Unrecoverable Rejects:
- If rejected products cannot be reworked or salvaged, determine appropriate disposal methods in compliance with environmental regulations.
- Dispose of unrecoverable rejects responsibly, ensuring minimal impact on the environment.
Responsibilities:
All employees involved in the production and quality control process are responsible for adhering to this SOP and reporting any deviations or issues to their supervisor.
Review and Revision:
This SOP shall be reviewed periodically to ensure relevance and effectiveness. Any necessary revisions shall be made with approval from management.
Conclusion – How to Create an SOP Document
Knowing how to create an SOP document without falling into the pitfalls requires diligence, collaboration, and a commitment to clarity and accuracy.
By understanding the purpose, identifying common pitfalls, and employing effective strategies, businesses can create SOPs that serve as invaluable tools for streamlining operations and driving excellence.
Remember SOP creation is an ongoing exercise, but with perseverance and attention to detail, excellence can be achieved.
Related Articles
- How to Create a Standard Operating Procedure that Works
- 10 Big Problems from Absence of Standard Operating Procedures
References
Hayton, E (2022) Why are SOPs Important? https://scribehow.com/library/why-are-sops-important