Do you want to know why implementing a quality management system (QMS) can guide you on how to reduce risk in the corrective action process?
The QMS is a structured approach to managing your business processes and activities to ensure that products or services not only consistently meet customer requirements, but comply with relevant regulations and standards.
The corrective action process on the other hand is a mechanism that is triggered when something goes wrong. It acts as your safety net, ensuring that a quality issue or non-conformance that arises is immediately addressed and rectified.
But, here is where risk reduction comes into play. Just as a well-designed safety net is woven with strong material, your corrective action process needs to be strengthened with strategies to prevent further glitches.
You may also think of it as fine-tuning the engine of a high-performance car (your business) to reduce the likelihood of any unexpected hiccups.
Root Cause Analysis and How to Reduce Risk in the Corrective Action Process
The key is to uncover the root cause behind the issue – whatever it is. Instead of a mundane checklist approach, use a more dynamic analysis.
This involves probing deep into cause-effect relationships, making use of techniques like the 5 Whys or Fishbone Diagrams. This not only resolves the immediate concern but also minimizes the chances of recurrence.
A QMS facilitates proper root cause analysis by providing templates and methodologies to identify the underlying reasons behind the issues. This approach ensures that corrective actions address the fundamental problems rather than just treating the symptoms.
Use Standardized Documentation for Future Precision
In the world of quality management, documentation is like your GPS navigation system. Keep track of the entire corrective action process – from initial identification to resolution.
The QMS provides a standardized framework for handling corrective actions. It establishes clear procedures and guidelines for identifying, documenting, and addressing issues.
Standardization reduces the chances of errors, miscommunication, and missed steps during the corrective action process.
Detail out the steps taken, responsible parties, and timelines. This is your blueprint for risk reduction, ensuring consistency and providing insights for future enhancements.
Document Control in Risk and Corrective Action
The QMS includes document control mechanisms that ensure the relevant corrective action procedures, policies, and guidelines are easily accessible to all stakeholders.
This prevents confusion and outdated information, reducing the risk of incorrect or ineffective actions being taken.
Engage the Team in Risk and Corrective Action
Gather your designated quality champions and engage cross-functional teams. This not only brings diverse perspectives but also encourages shared ownership of the solution. By doing so, you are tapping into a treasure trove of collective wisdom and experience.
Rank and Prioritize Risk
To incorporate risk into the corrective action process requires that you consider the potential consequences and likelihood of recurrence for identified issues.
By doing so, you can prioritize corrective actions based on the level of risk they pose. Keep in mind that not all issues are created equal.
Use a risk-ranking system that categorizes issues based on their potential impact and occurrence probability. This way, you can consistently channel your limited resources to address the most critical concerns first.
8 – Step Method to Risk Reduction
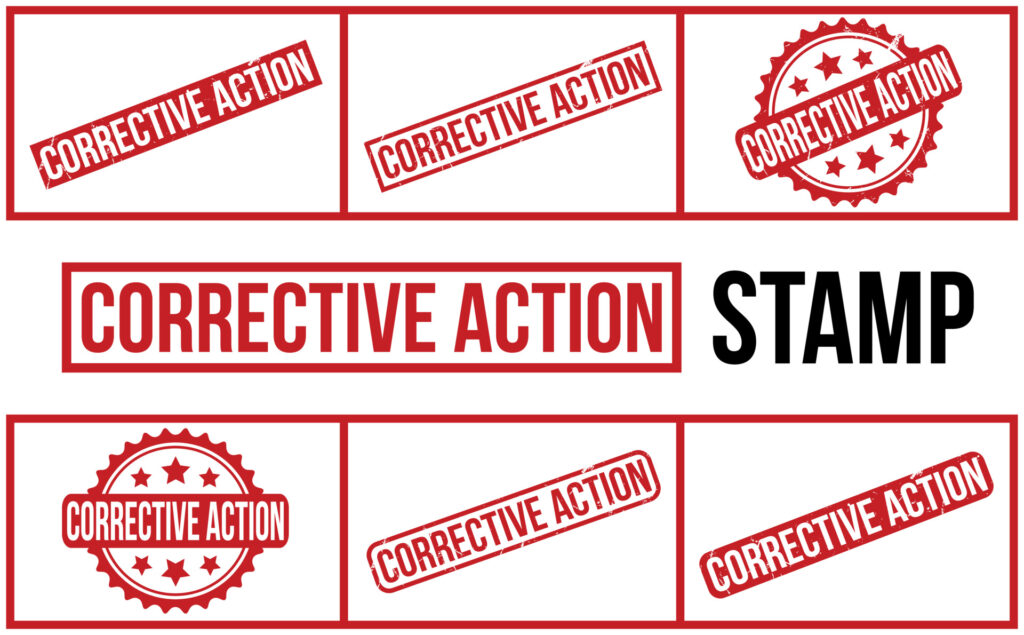
Within the QMS, risk assessment tools can be integrated to evaluate the severity and potential impact of identified issues. By prioritizing corrective actions based on risk levels, resources can be focused on addressing high-risk problems first, minimizing the chances of major quality or compliance incidents.
1. Identify Risk
During the issue identification phase, assess the potential risks associated with each problem. Consider the impact on product quality, customer satisfaction, safety, compliance, and business reputation. Categorize issues based on their severity and potential consequences.
2. Assess Risk
Conduct a risk assessment to determine the likelihood of the issue occurring again and the potential impact if it does. Use tools such as risk matrices or qualitative/quantitative risk analysis techniques to assign a risk score to each problem.
3. Prioritize Corrective Actions Based on Risk
Prioritize corrective actions based on the risk assessment results. High-risk issues with severe consequences and a higher likelihood of recurrence should be addressed as a matter of higher priority than lower-risk problems.
4. Conduct the Root Cause Analysis with a Risk Perspective
During root cause analysis, consider how each identified root cause contributes to the overall risk. Addressing root causes that have a higher impact on risk will result in more effective corrective actions.
5. Develop an Action Plan
Develop an action plan that take incorporates risk. Ensure that actions target not only the immediate symptoms but also the underlying causes that pose the highest risks.
6. Develop an Escalation Process for High-Risk Issues
Establish an escalation process for high-risk issues, ensuring that they receive attention from higher management or specialized teams. This helps prevent critical problems from being overlooked or delayed.
7. Allocate Resources Based on Risk
Allocate resources according to the level of risk associated with each corrective action. High-risk issues may require more attention, expertise, and resources.
8. Access Effectiveness
Implement a robust monitoring and verification process to assess the effectiveness of corrective actions in reducing risk. Regularly review progress and ensure that actions are achieving the desired risk reduction.
Continuous Monitoring
Quality management is not a one-time exercise, but a process that requires constant attention. Set up a mechanism to continually monitor and evaluate the effectiveness of corrective actions implemented.
This will ensure that any unforeseen consequences or evolving situations are swiftly addressed. It also helps identify areas for improvement to reduce further risk.
Leverage Technology for Efficiency
Embrace technology to streamline your corrective action process. Quality management software and tools can help track, analyze trends, and automate notifications and reminders for various stages of the corrective action process.
This ensures that responsible individuals are promptly informed about their tasks, reducing the risk of delayed actions. With a QMS, corrective action activities are tracked and documented at each stage.
This traceability ensures accountability and helps monitor the progress of corrective actions. It becomes easier to identify bottlenecks, delays, or deviations from the plan, allowing for timely intervention.
Conclusion – How to Reduce Risk in the Corrective Action Process
Knowing how to reduce risk in the corrective action process is not just about providing a quick fix to what is broken, but about building resilience and agility into your quality management system.
This helps to proactively address high-risk issues, allocate resources wisely, and reduce the likelihood of recurring problems with significant consequences.
Need assistance with risk assessment, corrective action or your quality management system? CONTACT US TODAY
Related Articles
- How to Perform Corrective Actions That Work – Remove Roadblocks
- Why Root Cause Analysis is Important for Continuous Improvement
References
Complete Guide to Corrective action vs Preventive Action – https://advisera.com/articles/complete-guide-to-corrective-action-vs-preventive-action/