As a small business owner, you have probably heard of the importance of a quality management for small business. You might believe that you have integrated quality management into your daily operations, but, are you doing it right?
Quality management is essential to ensure that your products and services meet customer acceptable standards. This can tremendously improve your reputation in the market.
This article explores quality management principles and provides seven steps to create a quality management system for your small business.
What Is A Quality Management System For Business?
Quality management refers to the process of continuous improvement for organizations, with the goal of meeting customer requirements and expectations and involves both quality assurance and quality control.
Quality assurance ensures that products and services meet the desired standards, while quality control focuses on the prevention and detection of defects in products or services before they reach customers.
Quality management is important because it can help small businesses maximize efficiency, create consistency, build trust with customers and employees, and increase profitability.
It also helps to identify opportunities for cost savings and potential revenue streams and help small businesses develop competitive advantage by providing more consistent products that customers can rely on.
Why Is A Quality Management System Important in Small Business?
Implementing a Quality Management System (QMS) is key to helping your business reach its fullest potential and gain numerous benefits. From improved customer satisfaction to greater efficiency and cost savings, here are five of the top advantages of a QMS:
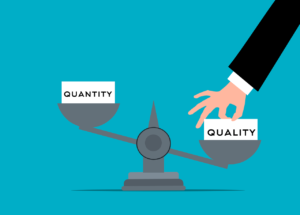
- Improved Customer Satisfaction: Ensuring that products and services meet customer expectations in terms of quality and reliability can help build customer trust and loyalty, resulting in repeat business and positive reviews.
- Increased Efficiency: With a QMS, businesses can streamline processes, reducing the time and resources needed to complete tasks which can bring cost savings.
- Reduced Waste: Waste can be greatly minimized in all areas of your business, from production to customer service, as unnecessary processes and materials will be cut out.
- Improved Productivity: With all processes running smoothly and efficiently, employees are better able to focus on essential tasks, allowing for improved productivity and faster turnaround times.
- Greater Employee Engagement: A QMS encourages an atmosphere of quality and excellence, helping to motivate employees by emphasizing how their work contributes to the success of the company.
Six Quality Management Principles
Six Quality Management Principles provide the foundation for any quality management system:
Why Is A Quality Management System Important in Small Business? – Start With Customer Focus
All activities within a company should be directed toward meeting the customer’s needs. Companies should strive to meet and exceed customer expectations by listening to their feedback and incorporating it into decisions about products or services.
Leadership
Company leaders lead by example for their employees to follow. They must ensure quality products and services are consistently delivered, stay informed on industry trends, and be open to feedback from customers and staff.
It is not enough to “talk the talk” without follow up!
Engagement
There must be adequate engagement with customers before and after-sales. This helps to understand customer needs, offer guidance, and being available for questions or troubleshooting.
Customer feedback and employee ideas, suggestions, and concerns can then be used to make decisions about quality management procedures.
Process Approach
This involves breaking down a system into individual processes to identify problem areas and find solutions that address the core of the issue. Creating standard operating procedures also helps to guarantee consistently high results.
Improvement
Companies must also seek ways to improve products, services, processes, and systems based on customer feedback, industry practices, or emerging technologies.
Problem-solving and root-cause analysis should be implemented to address problems effectively instead of temporary fixes and, learning opportunities must be offered to employees for continual learning and growth.
Evidence-based Decision Making
Decisions should be based on data gathered throughout product development or delivery processes. This data can be used to locate weak points for improvement.
Workshops, surveys, and activity logs are some data sources that help create an evidence-based approach that allows making informed decisions quickly while avoiding costly mistakes or missed opportunities.
These six Quality Management Principles are key elements of any quality management system which help companies deliver superior products and services that meet customer needs while standing out from competitors.
How To Develop A Quality Management System – What Should a Quality Management System Include?
Creating a quality management system does not have to be complicated or time-consuming. Follow these 9 simple steps below to develop one for your small business:
1. Create a Written Document That Defines Quality
Quality can be defined differently, depending on the organization’s goals and the type of product or service they provide.
Creating a written document that outlines your organization’s quality objectives and standards is essential for setting expectations and guiding employee behavior.
This document should describe how quality is measured and monitored and should be shared with all employees so that everyone is on the same page.
2. Organize Structure, Functional Roles & Responsibilities, and Reporting Structure
Developing an organizational structure that outlines each employee’s roles and responsibilities is necessary to ensure that everyone is working towards the same goals.
This document should also describe the reporting structure so that employees know who to contact for help or provide progress updates. Ensure that you create accountability for your processes so that you know who to address for any mishaps.
3. Define the Core Processes
Defining the core processes of the organization is key for successful quality management. First, identify the processes that are essential for achieving quality, such as product development, customer service, and operational processes.
Next, develop detailed procedures and work instructions that clearly outline how each process should be completed.
4. Develop Quality Documents
Developing quality documents such as procedures, work instructions, checklists and job descriptions is essential to ensure that employees follow the correct processes and procedures.
These documents should describe in detail the steps needed to complete the process and be updated regularly to reflect any changes. Once again, there must be individuals tasked with accountabilities.
5. Develop Quality Controls
Quality controls are essential for monitoring and improving the quality of the organization’s products and services.
Identify which processes need to be monitored and create a system for collecting and analyzing data. This data can then be used to identify deficiencies in the system for appropriate changes to be made.
6. Document Management System
Creating a document management system helps ensure that documents are up-to-date and easily accessible. This system should include the ability to track changes, set expiration dates, and provide secure access to all documents.
7. Quality Training for Employees
Providing quality training for employees is essential for ensuring that everyone is aware of the organization’s quality objectives and processes. Create training programs that focus on the organization’s core processes.
8. Collect and Manage Data
This data includes customer feedback, customer satisfaction surveys, market research, and other information related to product and service quality.
Identify which data should be collected for analytics, and store in a central repository in an organized way that allows for easy access and analysis.
9. Reward and Recognize Good Performance
Quality performance should be rewarded and recognized. This can be done through monetary rewards, recognition programs, and other forms of recognition.
Incentives will ensure that employees improve their own performance to better overall business performance.
Conclusion – What Is A Quality Management System For Business?
Developing a quality management system for small business is necessary for a business looking for continuous improvement opportunities. These can come from cutting costs, reducing waste, increasing customer satisfaction, or increasing market share.
By understanding quality management principles and following the 9 steps outlined above, you can start developing an effective QMS for your small business today!
Better still, let us help you get started and Contact Us Here
Related Articles
Create Business Systems – Learn How to Move From Chaos to Clarity
References
The Ultimate Guide to Implementing a Quality Management System In Your Company. – SweetProcess