Integrating root cause analysis and quality management systems can move your business up the ladder of excellence as they both work hand in hand – like Siamese twins – to drive quality and efficiency.
Integration provides several benefits that can result in improved product or service quality, customer satisfaction, and overall business performance.
This article provides a review of some key benefits -business performance, customer satisfaction, risk management and regulatory compliance, and, standardization. Read this article for How to Integrate Them.
Benefits of Integration
These are business performance, customer-related benefits, risk management and regulatory compliance, and standardization.
Business Performance is Enhanced by Root Cause Analysis and Quality Management
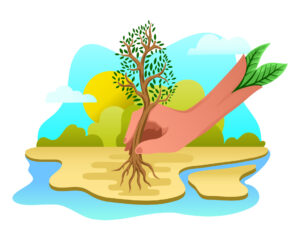
There is no doubt that business performance is one area of business that significantly improves with the conduct of a root cause analysis It does the following:
Identifies and Addresses the Underlying Causes of Quality Issues
It does this with targeted corrective and preventive actions (CAPA) , preventing them from recurring.
Improves the Decision Making Process
Armed with a deeper understanding of why issues occur based on analyzed data you can make make more informed decisions about necessary corrective actions such as process changes, resource allocation, and quality improvement strategies based on insights into trends and patterns..
By resolving root causes, you reduce the likelihood of similar problems happening in the future.
Root Cause Analysis and Quality Improvement Reduces Waste
Instead of applying resources to address symptoms, you focus them on solving the actual causes. This optimizes the use of both human and financial resources.
When you analyze incidents or near-misses through RCA, you uncover the underlying factors that led to the risk event. This knowledge allows you to proactively put preventive measures in place.
You can strengthen your processes, train your team, and implement safeguards to ward off potential risks.
Useful for Strategic Planning
The insights gained from RCA can inform your strategic planning. You can then process to prioritize business initiatives based on the most critical root causes and align your business goals accordingly.
Continuous Improvement
The RCA process encourages a culture of continuous improvement through a methodical analysis of issues from which you can then use the findings to make targeted enhancements to processes and operations.
Creates a Repository of Historical Lessons Learned
Creates a library of lessons learned from past issue help with quickly tackling similar problems should they occur again in the business.
Experience they say is the best teacher, and this is so true of the lessons learned for a root cause analysis, PROVIDED that you have kept reference documents of them. If not, it is just “shadow boxing”!
As you document your RCA findings and solutions, you are creating a repository of valuable information. When similar issues arise in the future, you can very quickly source information from this repository to implement proven solutions quickly.
Customer Related Benefits
There are at least five customer related benefits that are derived from integration of the RCA with the QMS. These are:
Transparency – Integrating RCA into your QMS encourages transparency in identifying and addressing issues. This transparency can positively impact relationships with customers, suppliers, and stakeholders.
Customer Satisfaction – Consistently resolving issues through RCA leads to improved product or service quality. Satisfied customers are more likely to be loyal, recommend your business to others, and provide positive feedback.
Cost Savings – Addressing root causes leads to more effective solutions, reducing the need for frequent fixes. This saves both direct costs (e.g., rework, warranty claims) and indirect costs (e.g., lost productivity, customer dissatisfaction).
Competitive Advantage – Demonstrating a commitment to quality improvement through RCA can set your business apart from competitors and enhance your reputation with customers.
Employee Engagement – Involving employees in the RCA process fosters a sense of ownership and engagement. Employees become more proactive in reporting issues and suggesting improvements to enhance the product or service to improve customer satisfaction. .
Risk Management and Regulatory Compliance
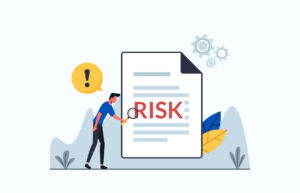
Risk Management – Identifying and addressing root causes can mitigate risks associated with quality issues, compliance violations, and safety concerns.
Every business faces risks—it’s just a part of the game. But instead of playing defense, you can use RCA to play offense and mitigate those risks effectively.
Regulatory Compliance – Many industries are subject to regulations and standards which require compliance or you end up facing penalties.
RCA can help you identify and correct deviations when they occur to ensure compliance with regulatory requirements.
Standardization – Root Cause Analysis and Quality Management in Action
Integrating RCA within your QMS promotes consistent and standardized approaches to problem-solving – processes, procedures, work instructions, checklists etc. This consistency ensures the smooth operation of your business as it grows.
By integrating RCA with your QMS, you create a structured approach to addressing quality issues that eliminates the “band-aid approach” and drives long-term, sustainable improvements.
Root cause analysis, IF used properly and consistently, will help guide your process improvement initiatives.
As you map out your processes, RCA will also help you identify inefficiencies and bottlenecks, allowing you to probe deeper to find out why certain steps are slowing things down or causing errors.
Related Articles
- Why Root Cause Analysis Tools and Techniques are Important
- How to Implement an Effective Root Cause Analysis – Plan
- Why Root Cause Analysis is Important for Continuous Improvement
- Benefits of Integrating Root Cause Analysis and Quality Management
Conclusion – Root Cause Analysis in Quality Management
Integrating root cause analysis with quality management is a game-changer. You harness the power of RCA to improve your processes, manage risks, and ensure that quality becomes the bane of your business.