A common question many businesses ask is how to measure a process and which key or good business metrics to use. Process metrics provide quantitative and qualitative statistics to assess and improve operational performance
. You can only make meaningful and informed decisions by using the right metrics for your processes.
Too many businesses tend to measure what is easy rather than what is important and necessary to help improve performance. Measure metrics related to your short-term and long-term goals to help assess how well the business is faring.
This article discusses key process metrics that can be used, but keep in mind that you only need to use those that are important for your business model.
What are Process Metrics?
They are measurements used to track the performance of a business process. Like key performance indicators (KPIs) they measure how a task performs and if it meets defined goals.
Process metrics provide information about process quality and typically run as a continuous improvement cycle. Keep in mind that broken processes can and will affect your results.
Process metrics can be useful in different businesses, and they are usually expressed as ratios or percentages that show the progress of the metric as a part of a whole.
What is a Business Process?
A business process is a strictly defined, repeatable unit of work that fulfills a business need. It could be any function a company needs to meet the expectations of its employees, stakeholders, or customers.
These can include tasks completed by humans or machines.
Why Process Metrics are Important
Process metrics provide valuable information at each stage of a business process. They help make more accurate decisions about innovation.
They can also increase production speeds and help with the measurement of company excellence. Regularly tracking process metrics may help a company be more transparent.
How to Measure a Process
Use the Supplier-Input-Process-Output-Customer (SIPOC) business process model. It is not as complicated as it sounds.
Because there are only a few process characteristics that can be measured, the choice of metric should be determined by the purpose of the business process within the overall system and business needs.
A group of process measures can be applied to any business. While different businesses have different process priorities, the best metrics for each business will be driven by their priorities and have a specific purpose towards improving performance of the process.
PROCESS EFFECTIVENESS
Process Effectiveness measures the performance of the process to the requirements of the customer. It is expected that every process should have a purpose geared towards an outcome that will satisfy the customer by solving their problem.
How well it does this is known as the effectiveness of that process.
Process effectiveness serves as one of the main sources of information for making well-founded decisions on better process management. Specifically, it allows decision makers to:
- Measure process performance
- Develop better management strategies and tactics.
- Plan for improvements.
- Conduct further process evaluations.
There are several measures of process effectiveness in relation to customer requirements. 10 of the simpler ones are presented below.
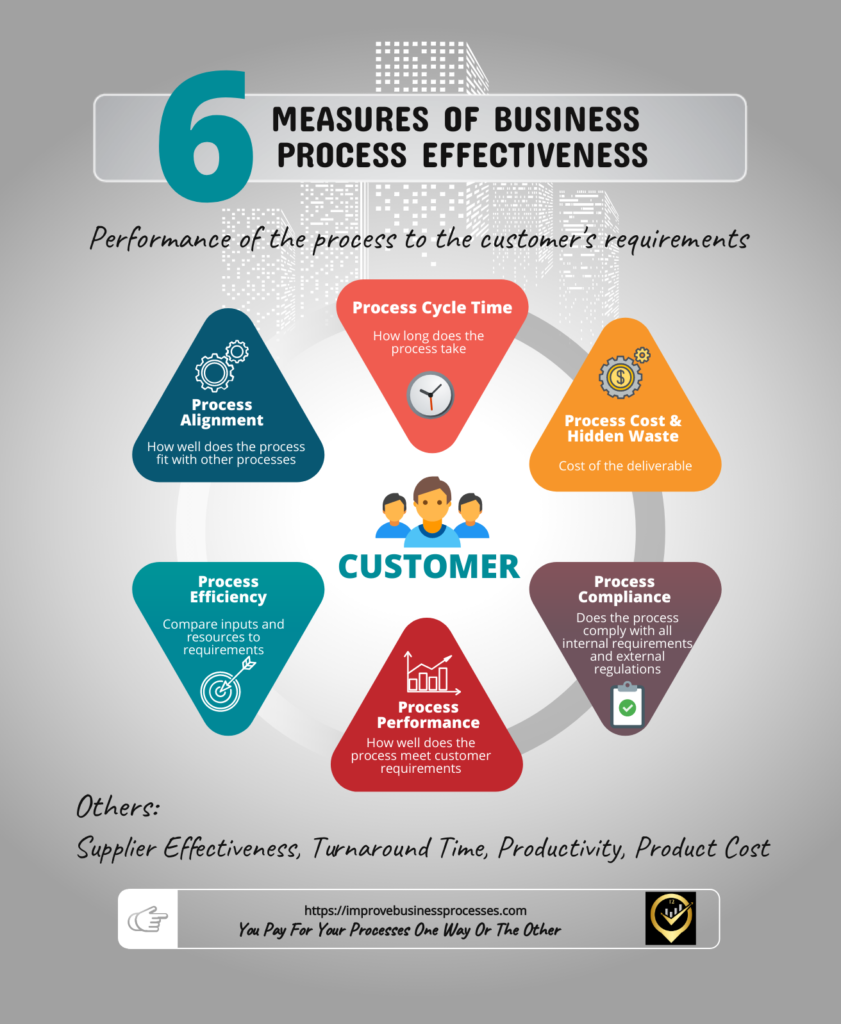
PROCESS MEASURES – How to Measure a Process
Aside for the 6 measures in the infographic above, there are at least another 4 measures that can be employed. These are turnaround time, supplier effectiveness, reliability, productivity, process (product) cost / hidden waste.
1. Process Alignment
Measures how well customer demand, inputs from the supplier, and the process outputs are synchronized. The ability of process output and supplier deliverables to meet the customer’s demand within their desired timeframe is a key metric.
2. Process Reliability
Specifically measures the ability of supply to meet demand requirements.
3. Process Cycle Time
This is the amount of time it takes to complete the entire length of a process from beginning to end. It measures the time from placing an order with the supplier to supply the required inputs to when the outputs (finished products or services) are delivered to the customer.
4. Process Efficiency – How to Measure a Process
Measures the inputs and resources used in the process compared to established standards.
Efficiency is the ratio of an input to an output. It is how quickly you can get something done with accuracy, or the best way to make something with the least number of resources. Measuring efficiency can tell you how much waste exists in the production cycle.
Lowered efficiency in a business result in higher costs (often leading to non-competitive prices), less reliable and dependable products and services, and slower response time
5. Process Compliance
This measure addresses compliance to third-party standards – regulatory, safety and environmental requirements, mitigation of corporate risk, and active management of the business process maturity and improvement.
Although the business may serve its customers effectively, efficiently, and profitably, it must also measure that it is doing so in a responsible and sustainable way.
6. Process Performance – How to Measure a Process
Measures how well the process meets customer requirements
7. Productivity
Measures how much of a process can be completed within a time period (x hours). It is usually represented as a ratio showing how much has been produced and the resources used to do it, and is especially useful for making comparisons between employees, techniques, or processes.
Businesses acquire assets for the sole purpose of using them to produce profits. Assets include people, tools and equipment, facilities, information technology, and intellectual property. Few businesses evaluate how much assets consumed by a process are used productively.
8. Product Cost
Measures the total cost to produce and deliver an output (product or service), including inputs, processing, and resource costs. This is called the cost of goods sold.
9. Supplier Effectiveness
Measures supplier performance to specified process requirements and customer needs. A common problem in operations is the failure to properly specify process needs from suppliers to meet customer specs / deliverables.
10. Turnaround time
The turnaround time measures how long it takes to fill a customer’s request from placement to delivery. You often measure turnaround time from the customer’s perspective
Improve Process Metrics
Determine Purpose of the Process
Determine what you’re trying to accomplish by measuring your processes. A SIPOC diagram (suppliers, inputs, process, outputs, and customers) shows how they interact with one another.
Train Employees About Processes
Employee buy-in and training will help with understanding the process metrics, and how to and track them. Know that omitting this important step will breed disgruntled employees.
Use a Process Metrics Software if Appropriate
Many software programs allow tracking of process metrics in one location. To identify suitability, conduct research into different programs to see what type of services they offer.
Conclusion
Understanding how to measure a process and identifying key business metrics to use will help in making make more accurate decisions about innovation, increase production, and improve measurement of company excellence.
If you found this article useful, kindly leave a comment for us. Need Assistance?
References
BPI Process Effectiveness Measurements https://www.managementstudyguide.com/flow-charts-and-quality-control-tools.htm